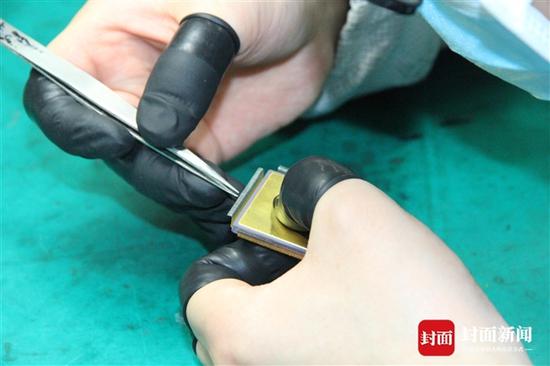
短時間專項攻關
“0”備料挑戰“100%”成功
早在2013年,嫦娥五號產品預先研究的攻關階段,研制團隊就發現了很多“嫦五”產品的“特殊性”。印制板單板面積較大、器件組成復雜、涉及種類多且密度大,這些都給產品的研制過程帶來了不小的挑戰。“僅我負責的一塊印制板,硬件成本就近200萬,比我自己的全部身家都要貴。”操作者明萬平笑著說道,“衛星產品的制造過程很特殊,涉及到的物料都很貴重且不易采購,我們沒有一個備料,也不容許哪怕一點點的失敗。”
由于嫦娥五號產品的特殊性,需保證在有限的時間內完成規定的焊接作業。在人工焊接難以保證焊接時間的情況下,公司大膽進行了生產線自動化焊接的探索工作。
為了使散裝物料能夠被全自動貼片機準確地吸取同時避免拋料、壓力損傷等問題,研制團隊進行了專項攻關,設計制作20余種專用散料托盤,摸索出了一組貼片機吸嘴壓力參數,首次實現了衛星產品某器件的自動化焊接一次成功。
按照此方法,團隊不僅大大提升了生產效率,同時保證了產品的焊接質量和一致性。“沒有備料,我們必須一次成功。那個時候大家都憋著一口氣,心想著一定要實現物料的100%一次焊接成功。”操作者周坤介紹。
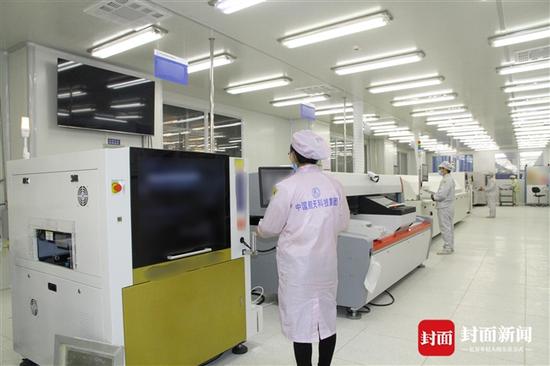
摸索出獨門絕技
讓器件能夠經受住不同溫度下的“冷熱煎熬”
嫦娥五號研制涉及某些特殊器件,如某種芯片裝焊的裝聯工作。“此類器件引線數多達256根、引腳厚度僅有0.13mm,焊接后需保證每個引線與焊盤間的焊料厚度控制在規定的范圍內,且要經受-55℃到+100℃的高低溫試驗保證不開裂。為達到這一技術指標,要求芯片一次成形成功,確保引線共面度小于0.1mm。“面對這個情況,全國技術能手何苗都倍感壓力。“每個廠家采用的引線材料還不盡相同。要確保每次成形都一次成功且滿足共面度要求,差一點都不行,這難度可想而知。”工藝楊喆麟補充道。
成形僅是完成了芯片裝焊準備工作的第一步,如何確保256個焊點全部一次焊接合格并且能夠經受極其嚴苛的環境試驗考驗,又是另一個更大的難關。技能骨干鄭奎每每回憶起當年的攻關時光都忍不住要感嘆一番。“為了適應‘嫦五’產品極高的試驗要求,我們焊接的時候都要打起十二分的精神,一點都不能錯、一度都不能差。”
為了生產時一次達到要求,研制團隊經歷數十次的反復研究和試驗,終于摸索出了一整套自己貫穿該芯片裝聯全流程的工藝方法和操作絕招。從器件成形到器件搪錫再到器件焊接,整個過程研制團隊靠著自己獨門訣竅,硬是把芯片的裝配工作整得“巴巴適適”,讓產品能夠穩妥可靠地經受住一次又一次的高低溫試驗“冷熱煎熬”。
“嫦娥五號傾注了很多技術人員的心血。為了嫦娥五號,他們有時把家都安在了工位上。看到嫦娥五號順利返回,作為親自參與過的航天人,大家有種不一樣的成就感。”黨支部書記楊明笑著說道。
劉帥 封面新聞記者 楊晨